Overview
SapphiroScan™ is the world-leading product for the fully automated detection of material defects in watch sapphire covers. The SapphiroScan™ scans non-polished watch covers and accurately maps all the defects, regardless of their type, size, and location. This unique process is performed quickly and automatically without the need for polishing of the covers. Defective pieces are automatically eliminated before the grinding and the polishing, which increases the production yield. Unlike manual quality inspection, SapphiroScan™ provides objective quality control and operates independently of the operators’ skill.
How it helps
- Automatic detection and removal of defects before costly processing.
- Early warning of the growth process drift through high sensitivity production monitoring.
- Objective and unambiguous quality grading allowing for factual quality discussions and smooth relations with customers.
How it works
The device inspects unpolished sapphire such as watch glasses and wafers for internal defects – including bubbles and clouds (see defect examples). Pieces to be tested are automatically picked from the input tray by a robot and passed through the inspection process. After inspection, the system decides automatically whether the piece is a PASS or FAIL (or other categories as set by the operator) and puts it in the respective output tray.
The automatic defect recognition performed on each piece is recorded to collect the geometric parameters of defects. This permits the collation and analysis of accumulated defect statistics.
SapphiroScan™ offers several quality control scenarios which may be further customized depending on the client’s requirements:
Sorting Mode. Fast raw material grading for large scale production, and for comparing the quality of batches. Automatic defect marking for each piece, and sorting to output trays according to the client’s quality control specifications. Ensures that only high-quality material is processed further. Allows working with multiple quality control specifications.
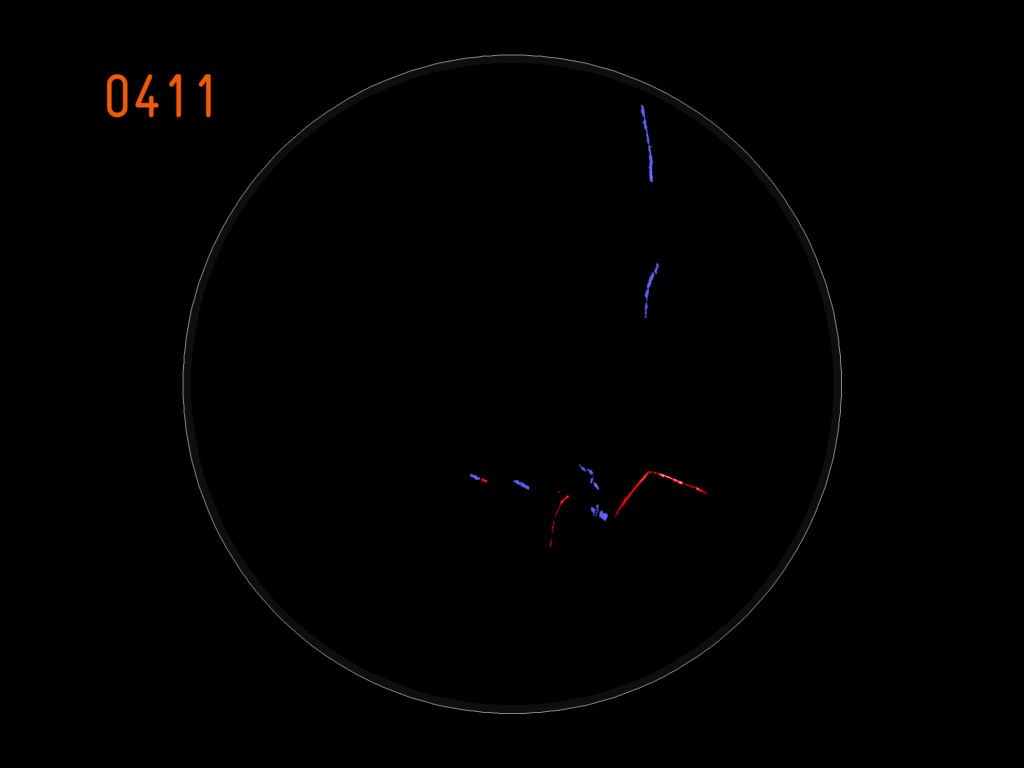
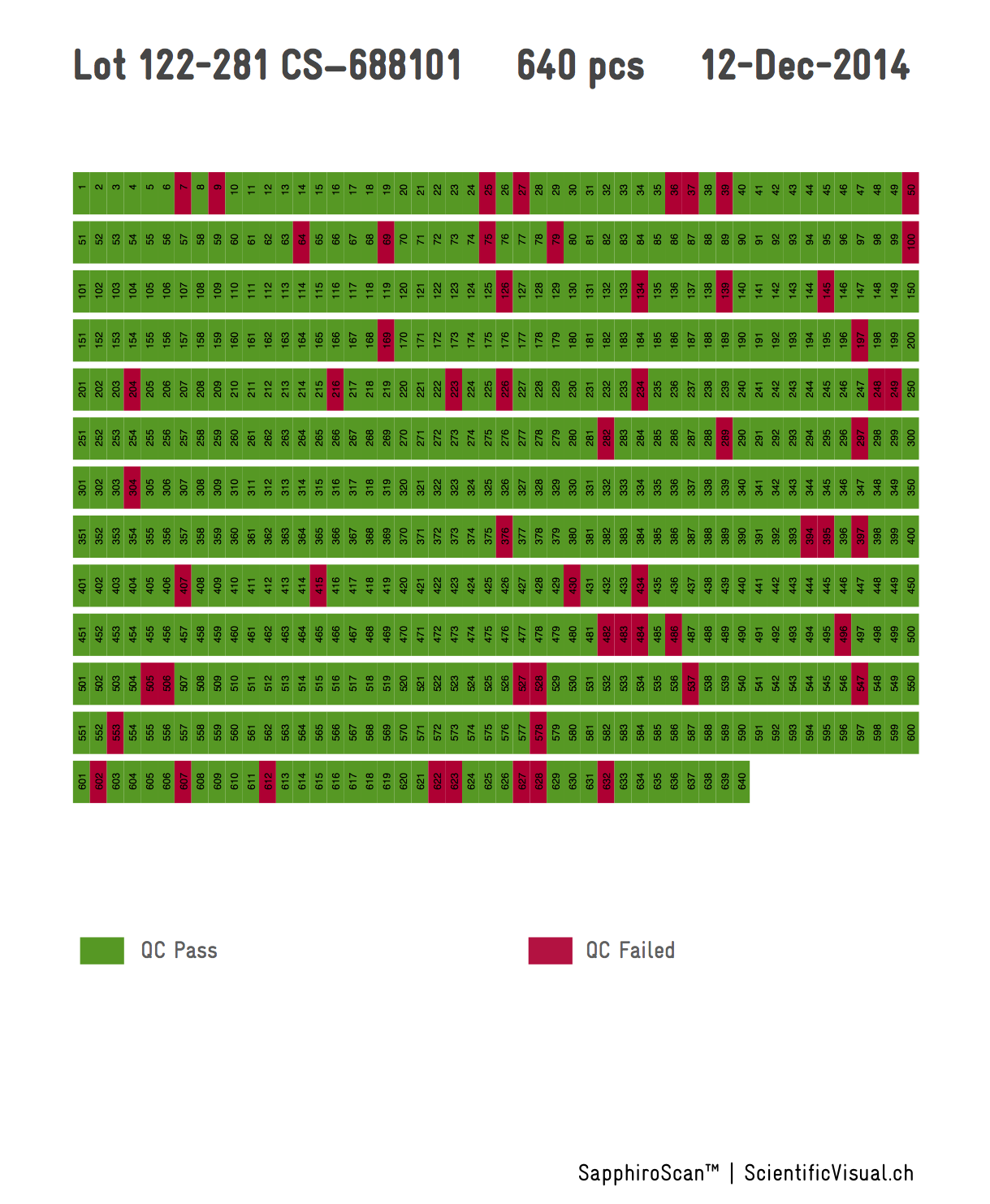
Tomography mode. Automated in-depth Z- scanning, which allows the building of a 3D model of each piece’s interior. It may be used for testing incoming material to be used to make particular pieces, and for analysing the morphology of specific defects.
3D Optimization Mode. Creates a 3D model of production pieces that may be produced from the pre-form as a result of accurately mapping its defects. Allows selection from multiple 3D models of production pieces. Inspected material is sorted into output trays according to usability for specific applications. For use in the production of sophisticated shapes to optimize yield.
Advantages
Sapphire manufacturers commonly rely on human eye quality tests to identify material defects in sapphire watch covers. However, SapphiroScan™ automated quality control can provide even greater accuracy, application flexibility, and cost efficiencies. Automated testing is particularly useful in combination with refractive index-matching technology, where grading the defectiveness of unpolished material is critical. The technology renders the rough sapphire surface transparent so that the interior of the material can be inspected without incurring the expense of polishing it.
Although this method is not new, it is too costly, complicated and inflexible for common use. But Scientific Visual’s recent hardware and software innovations using computer-controlled automation mean manufacturers can now determine a multitude of defect parameters in unpolished blanks, including their exact XYZ position, relative visibility to the human eye, and general defect size and morphology. And all this with just one automated test!
Practically speaking, the higher the processing costs (rounding, grinding, polishing), the greater the savings that clients can realize by the preliminary scanning of raw materials entering their production process.
Check your Return-on-Investment instantly with our ROI calculator online.
Dimensions
741 x 741 x 895 mm (WxLxH). Weight 70 kg
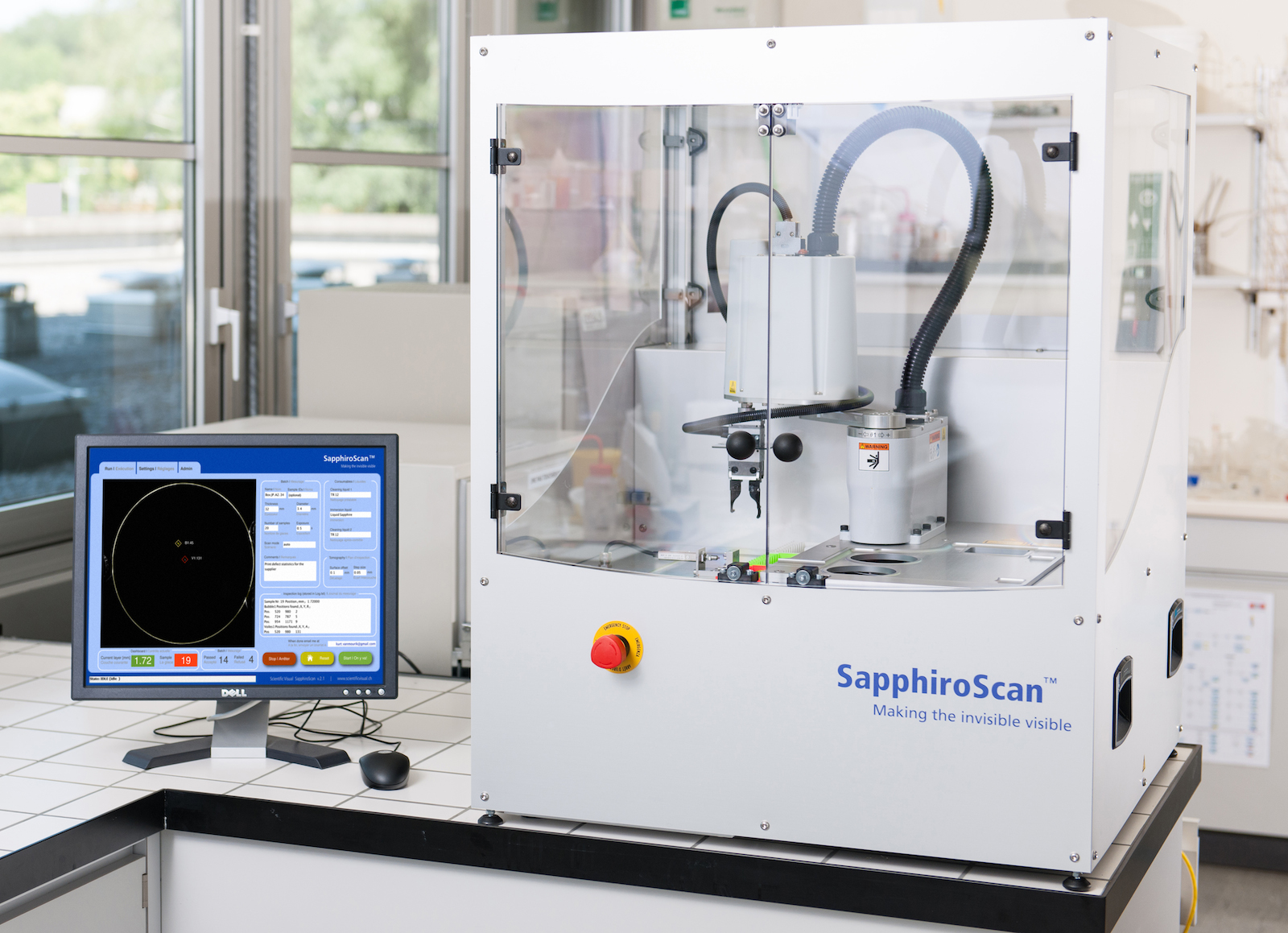
Downloads
![]() |
Brochure: SapphiroScan™ for the watch industry |